How to Save Energy in your Hotel: Comfort Controller Case Studies
Where should you look to make big energy savings at your hotel? Your first area to focus on is the energy used to heat/cool your guest rooms and public areas. This will most likely represent 60% of your total energy consumption. In this article we will demonstrate how much is wasted and how you can make significant savings.
Causes of wasteful energy use:
- Guest misuse of the controls leaving heating on or cooling to extremes
- Leaving systems on when guests have left room/apartment
- Lack of guest understanding around how to save
- Accessibility to control system (radiator valves in obscure location)
- Guests can circumnavigate key tags!
- Management worried about guest experience and leave systems on long before guests arrive
- Lack of synchronisation between guest arrival time and having the room heated
- No or low maintenance
- Lack of an intelligent system to adjust to outside conditions
- No synchronisation between heating/cooling and use of natural ventilation
- No or limited policies and training for staff
Cost of improving the situation is a barrier, such as the cost of installing a building management system. This can be very high because it requires retrofitting wired control and a computer system which is customised. The capital expenditure can be too high and the disruption too large, which is why only 10% of hotels in Europe have one. Another problem is that many hotels and accommodation types are owned by a third party who are not interested in investing in building improvement and hotel management companies cannot justify the expense to install new equipment.
With our new responsible technology, we have an affordable solution that enables hoteliers to have maximum control and savings for an ROI in months. It is called the Comfort Controller and here’s the evidence.
CASE STUDY 1
In tropical North Australia, the Comfort Controller was implemented to control over 70 split-system air conditioning units. Given the climate, the key issue faced by the property is humidity, with policies in place for air conditioning in all room to be continuously on during the wet season. Best practice indicates when an inside space is above a threshold >60% humidity (ASHRAE-55), an intervention to control moisture levels must be applied to reduce risk of mold growth. Therefore, the requirement for Comfort Controller was to reduce the humidity in inside spaces to 60%, using the least amount of electricity required.
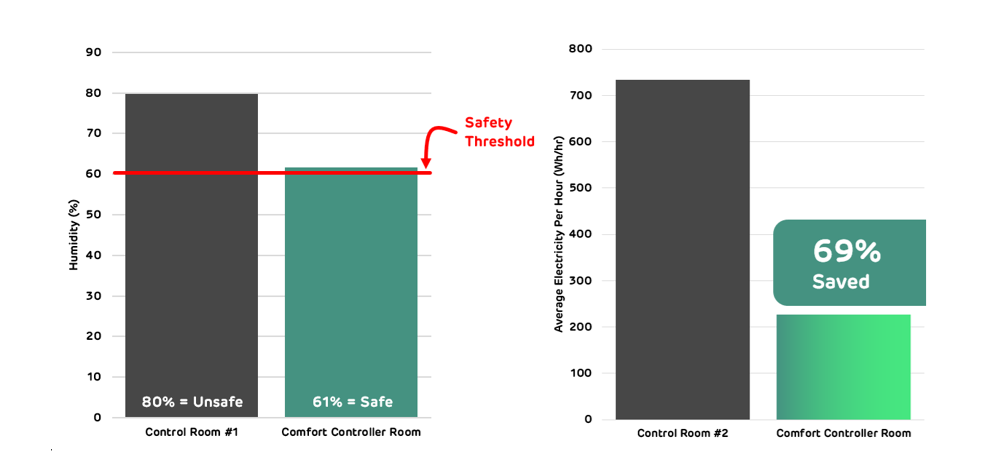
The results from the initial study conducted with Griffith University revealed an electricity saving of 69% during unoccupied periods, reflecting in tens of thousands of cost and carbon savings that can be made within the first year – covering the capital investment in a matter of months.
Putting this into practice, during the dry season when air conditioning is less required, year-on-year savings up to 96% in an unoccupied guest room was observed.
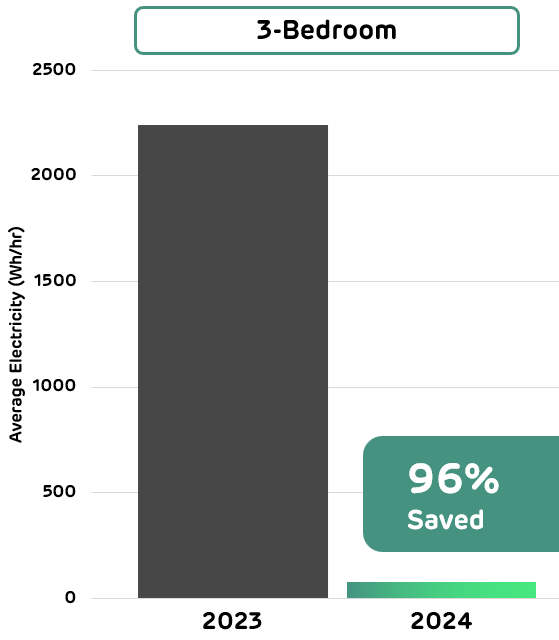
Through analysis of equipment energy use and operational maintenance behaviours, the Comfort Controller identified up to an additional 10% energy savings that can be made via routine preventative maintenance.
CASE STUDY 2
In Cumbria, in the north of the United Kingdom, the Comfort Controller was introduced to control central heating radiator units. Prior to implementation, operations found radiators would be left on throughout unoccupied periods, leading to uncomfortably high temperatures in empty rooms and significant energy waste.
The Comfort Controller saved the energy used in these radiators by more than 99%. Minimal gas was used to prevent frost in the radiator pipes to ensure the equipment is well maintained.
CASE STUDY 3
In a Sydney hotel, the Comfort Controller was installed for the fan coil air conditioning system in guest rooms. The system integrated with motion sensors applied in guest rooms to provide savings when unoccupied, as well as when rooms were occupied and vacant.
The Comfort Controller applied booster schedules, so when guests were due to arrive to their room in 30 minutes time, the room would reach its target temperature depending on the live inside and outside conditions and time of day.
Samples demonstrated that the Comfort Controller rooms saved 88% electricity compared to control rooms, without any compromise to guest comfort. As rooms met more optimal thermal comfort conditions for guests upon arrival (according to live conditions and guest origin – more information here), guests also used less energy to heat/cool their rooms when they were present in rooms.
These savings demonstrate a highly attractive ROI within months, as unnecessary energy use as well as overused and undermaintained equipment are mitigated.
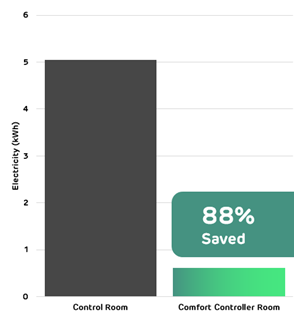
HOW CAN THE COMFORT CONTROLLER HELP YOU TO ACHIEVE ENERGY SAVINGS?
Comfort Controller makes it easy to run heating/colling systems:
- By saving you money immediately and offering an outstanding ROI in days, not years
- With human centered design making it simple for managers and guests to use
- Saving you time as staff do not need to control the heating/cooling manually
- Setting rooms to perfect conditions through booster timing prior to check-in
- Improves guest thermal comfort satisfaction as room temperatures are monitored in real-time for perfect conditions that don’t waste money
- Can be applied to any building type using split system, fan coil unit air conditioning, or central heating radiators in any global climate zone
We are so confident of our solution that we will install the equipment for a demonstration at no cost to you. Comfort Controller puts the control back in your hands (and your staff, guests), reduces staff time, and increases guests’ satisfaction. Contact us now to book your free on-site demonstration.
Click here to find out more about the Comfort Controller service.